JVN Bearings, Shop No F6,
1st Floor, Ruby Commercial Centre,
Mangalore, 575002
Ball Bearing Manufacturing Process
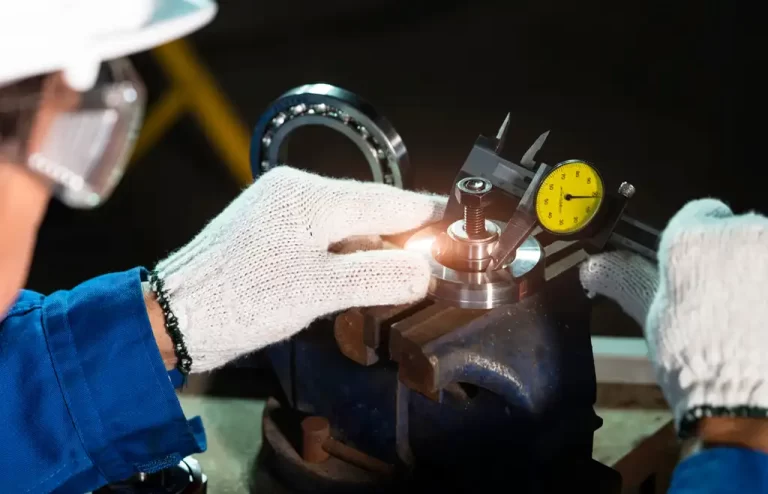
The manufacturing process of ball bearings typically involves several steps. Let’s break down the process step by step: Material Selection Wire Drawing Heading Cold Heading Heat Treatment Grinding Lapping Assembly and Packing It’s important to note that the specific ball…